What is Ceramic Sintering?
Ceramic sintering is a process in which ceramic powder or green body is heated to high temperature to densify it and form ceramic products with certain strength and performance. The following is a detailed introduction:Sintering process
- **Low temperature stage (room temperature - 300℃)**: It is mainly to remove the adsorbed water in the green body. The water in the green body gradually evaporates during the heating process, and the weight of the green body decreases, but the volume remains basically unchanged.
- **Medium temperature stage (300 - 900℃)**: Organic matter, carbonates and other impurities in the green body begin to decompose and oxidize, and the physically adsorbed water and chemically bound water on the surface of the ceramic particles are further discharged. The green body will shrink to a certain extent at this stage, and the strength will be improved.
- **High temperature stage (900 - 1300℃ and above)**: Ceramic particles begin to diffuse and rearrange significantly. The contact points between particles gradually form necks and continue to grow, so that the particles are connected to each other to form a network structure. At the same time, the pores in the green body gradually decrease, the density continues to increase, and finally reaches a higher density, and the various properties of the ceramic are basically formed.
- **Cooling stage**: Ceramic products sintered at high temperature need to be cooled slowly to avoid cracks or other defects caused by thermal stress. During the cooling process, the organizational structure of the ceramic will be further stabilized.
Sintering principle
- **Rearrangement of powder particles**: In the early stage of sintering, due to the adsorption force and capillary force on the surface of the particles, the powder particles will move and rearrange relatively, making the accumulation between the particles more compact and the porosity of the green body reduced.
- **Transfer and diffusion of substances**: As the temperature rises, atoms gain enough energy to begin to diffuse. The atoms on the surface of the particles migrate to the necks between the particles through diffusion, causing the necks to grow continuously and the bonding force between the particles to increase. At the same time, the grain boundaries will also move, promoting the removal of pores and the growth of grains.
- **Liquid phase sintering (some ceramic systems)**: For some ceramic systems containing flux or that can form a liquid phase at high temperature, the presence of the liquid phase helps the transfer of substances and the rearrangement of particles. The liquid phase can fill the pores between the particles, accelerate the sintering process, and improve the density and performance of the ceramic.
Purpose of sintering
- **Increase density**: Through sintering, a strong bond is formed between ceramic powder particles, the porosity is reduced, and the density of ceramics is increased, thereby improving its mechanical properties, thermal properties, electrical properties, etc. For example, dense ceramics have higher strength and hardness and can withstand greater external forces and pressures.
- **Improve performance**: The sintering process can make the crystal structure of ceramics more complete and uniform, eliminate internal defects, and thus improve the various properties of ceramics. For example, by controlling the sintering process, ceramics can have good insulation properties, thermal conductivity, optical properties, etc., to meet the needs of different application fields.
- **Give shape**: Sinter the formed ceramic body so that it can maintain its shape while obtaining sufficient strength and stability, and become a ceramic product with practical value.
Influencing factors
- **Raw material characteristics**: The particle size, shape, purity, chemical composition, etc. of ceramic powder have an important influence on the sintering process and product performance. Generally speaking, powders with fine particle size, regular shape, and high purity are conducive to sintering and can obtain higher density and performance.
- **Sintering temperature and time**: are the key factors affecting ceramic sintering. If the temperature is too low or the time is too short, the diffusion and bonding between the powder particles are insufficient, and the green body is difficult to achieve a high density; if the temperature is too high or the time is too long, it may cause excessive grain growth, green body deformation, or even overburning, which will reduce the performance of the ceramic.
- **Atmosphere conditions**: Different atmospheres have different effects on ceramic sintering. For example, in an oxidizing atmosphere, some ceramic components may undergo oxidation reactions; while in a reducing atmosphere or vacuum environment, the metal elements in the ceramic can be prevented from being oxidized, which is conducive to the sintering of some special ceramic materials.
Kejia's vacuum carbon tube furnace has shown significant advantages in the ceramic sintering process. In the low-temperature stage, the equipment accurately controls the temperature and stably raises the temperature from room temperature to 300℃, effectively removing the adsorbed water in the ceramic body and ensuring the stability of the body quality. Its high-precision temperature sensor works in conjunction with the intelligent control system to ensure minimal temperature fluctuations and avoid damage to the body due to unstable temperature.
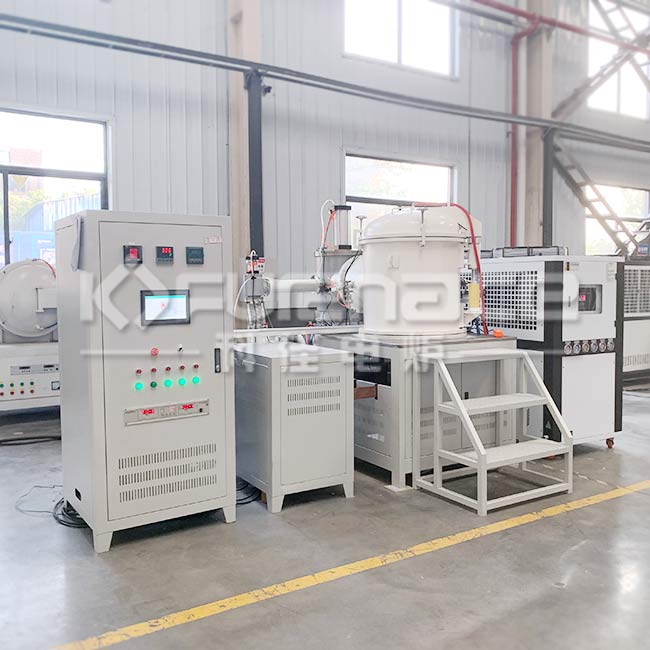
Entering the medium-temperature stage, from 300℃ to 900℃, Kejia's equipment, with its excellent temperature control performance, helps the organic matter, carbonates and other impurities in the body to fully decompose and oxidize, and the water in the body is further discharged. In this process, the uniform temperature field in the furnace makes the various parts of the body react synchronously and shrink to the same degree, laying a good foundation for subsequent sintering.
When the temperature rises to the high-temperature stage (900-1300℃ and above), the core advantages of Kejia's vacuum carbon tube furnace are highlighted. The high-purity carbon tube heating element provides a strong and stable heat output, so that the temperature in the furnace quickly reaches and maintains a high temperature range suitable for the diffusion and rearrangement of ceramic particles. The effective maintenance of the vacuum environment prevents the erosion of harmful gases on ceramics, greatly promotes the growth of the necks between ceramic particles, accelerates the removal of pores, and significantly improves the density of ceramics.
During the cooling stage, the cooling system carefully designed by Kejia equipment can cool the sintered ceramic products evenly according to the preset slow cooling rate, avoid cracks caused by thermal stress concentration, and ensure the integrity and internal structure stability of ceramic products. Through the precise control of the entire process of Kejia equipment, the ceramic sintering process can be carried out efficiently and stably, and the ceramic products produced have high density and excellent performance. They are excellent in mechanical strength, insulation, thermal stability and other aspects, meeting the stringent requirements for high-quality ceramics in many fields such as electronics, aerospace, and construction.
If you want to further explore the application details of Kejia equipment in other links, or compare the performance of different equipment in ceramic sintering, you can contact me at any time.