Core Process and Key Technology of Vacuum Furnace
Core process steps of vacuum furnaceVacuum extraction and sealing control
Start the vacuum pump group (such as mechanical pump, diffusion pump) to reduce the pressure in the furnace to the preset range (usually 10⁻³~10⁻⁶ Pa) to avoid oxidation reaction between oxygen and materials. The double-layer water-cooled sealing structure and high-temperature resistant materials (such as molybdenum and tungsten) are used to ensure the airtightness of the furnace body at high temperatures, and the air leakage rate must be lower than 1.33 Pa/h
Heating and temperature control
The electric heating element (such as graphite, molybdenum wire or silicon carbide rod) heats the workpiece by radiation, and the maximum temperature can reach 2200℃ (such as tungsten heating body)
The intelligent temperature control system supports multi-segment programming, real-time monitoring of temperature uniformity (within ±3℃), and optimizes the heating rate and insulation time through the PID algorithm
Cooling and quenching technology
High-pressure air-cooled quenching: nitrogen, argon or hydrogen is used as the cooling medium, and the pressure can reach 2000 kPa to achieve rapid and uniform cooling and reduce workpiece deformation
Oil quenching/water quenching: For special alloy steels, choose vacuum quenching oil or water cooling system to avoid hydrogen embrittlement on the material surface
Process type and customized process
Vacuum brazing: melt the brazing material in a vacuum environment and penetrate into the gap between the workpieces to form a high-strength connection, which is suitable for aircraft engine blades and electronic devices.
Vacuum sintering: densify powder materials through high temperature and high pressure, used for forming cemented carbide and ceramic composite materials.
Vacuum annealing/tempering: eliminate internal stress of materials, improve ductility and corrosion resistance, commonly used in titanium alloy and stainless steel processing
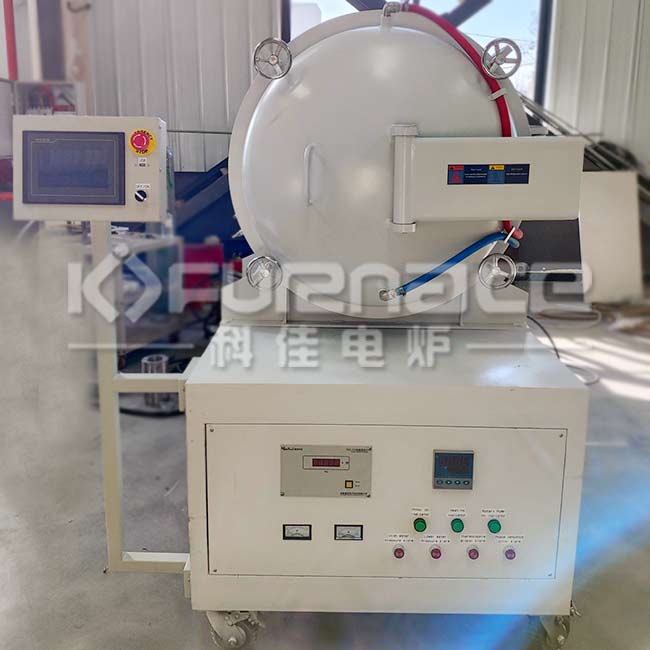
Process advantages and technological innovations of vacuum furnacesSurface quality and performance improvement
Non-oxidative decarburization: vacuum environment isolates oxygen, the surface of the workpiece remains bright, and no subsequent polishing is required.
Degreasing and degassing: volatilize grease and impurity gases on the surface of the workpiece at high temperature to improve the purity and mechanical properties of the material.
Energy-saving and environmental protection characteristics
Low heat loss design: using multi-layer metal radiation screens (such as molybdenum foil) and ceramic fiber insulation layers, energy consumption is reduced by 30% compared to traditional electric furnaces
Zero pollution emissions: no waste gas or waste residue is generated, in line with EU CE and ISO 9001 environmental protection standards
Intelligent and automated
Remote monitoring system: through PLC controller and touch screen interface, real-time adjustment of process parameters and data recording are realized, supporting NADCAP certification requirements.
Safety interlock mechanism: equipped with triple safety locks and automatic pressure relief valves to prevent accidents caused by hydrogen or nitrogen leakage
Application fields and typical cases of vacuum furnacesAerospace: vacuum brazing of turbine blades, vacuum solution treatment of titanium alloys.
Automobile manufacturing: vacuum carburizing of gears, vacuum quenching of engine parts.
Electronic industry: vacuum sintering of semiconductor materials, vacuum melting of high-purity metals.
Scientific research field: vacuum aging treatment of new alloys, vacuum annealing of superconducting materials.
Operation precautions and equipment maintenance
Process parameter optimization: adjust the vacuum degree, heating rate and cooling medium according to the material characteristics to avoid overheating or deformation of the workpiece.
Key points of equipment maintenance:
Regularly check the oil status of the vacuum pump to ensure that the pumping rate meets the standard.
Maintain the vacuum in the furnace or fill it with inert gas (such as argon) when shutting down to prevent moisture absorption and oxidation.
Emergency treatment: In case of sudden power outage, the emergency water cooling system must be started immediately to prevent overheating and damage to the furnace body.