A brief discussion on the calcined alumina powder process of Kj heating furnaces
Calcined alumina powder refers to the process of heating alumina powder at a certain temperature to change its physical and chemical properties. The process of calcining alumina powder usually includes the following steps:
Raw material preparation: Mix alumina powder according to a certain proportion to ensure the quality and stability of the raw materials.
Mixing: Mix the prepared alumina powder with other additives (such as fluxes, pigments, etc.) to ensure uniformity.
Molding: The mixed alumina powder is molded through a molding machine into green bodies of various shapes.
Sintering: The formed alumina body is placed in a high-temperature furnace for sintering, so that changes occur between the particles and a dense structure is formed.
Grinding: The sintered alumina body is ground to obtain the desired particle size and shape.
Calcining: The ground alumina powder is placed in a calcining furnace for high-temperature calcining, usually above 1000°C. The purpose of calcination is to remove residual organic matter and moisture and improve the crystallinity and stability of alumina powder.
Cooling: After cooling, the calcined alumina powder can be packaged and stored for downstream production.
The process of calcining alumina powder can be adjusted and optimized according to specific needs to achieve ideal product performance and quality. This process is mainly used to produce alumina ceramics, abrasives, fillers and other products, and is widely used in ceramics, electronics, chemical and other industries.
Calcined alumina powder usually requires the use of a high-temperature heating furnace for the calcination process. Commonly used high-temperature heating furnaces include:
Resistance heating furnace: The resistance heating furnace uses the heat generated by the resistance wire to heat the furnace, which can provide a high-temperature and high-purity atmosphere and is suitable for calcining powder materials such as alumina powder.
Gas heating furnace: The gas heating furnace heats the furnace chamber through the high-temperature airflow generated by the combustion gas, which can provide larger heating power and higher temperature. It is suitable for calcination processes that require rapid heating and high temperature.
Vacuum heating furnace: Vacuum heating furnace can be heated in an oxygen-free or low-oxygen environment, and is suitable for calcination processes that require controlled oxygen content.
Atmosphere controlled heating furnace: The atmosphere controlled heating furnace can control the atmosphere composition in the heating chamber and is suitable for processes that require calcination under specific atmosphere conditions.
Tubular heating furnace: The tubular heating furnace transfers the heat of the heating element through the pipe, which can achieve continuous heating and calcination and is suitable for mass production.
Kj heating furnaces can select appropriate models and specifications according to the requirements of the calcining process to ensure that the calcined alumina powder can achieve the expected heat treatment effect. When selecting a heating furnace, factors such as heating temperature, heating rate, heating uniformity, and atmosphere control need to be considered. If you are interested, please feel free to inquire.
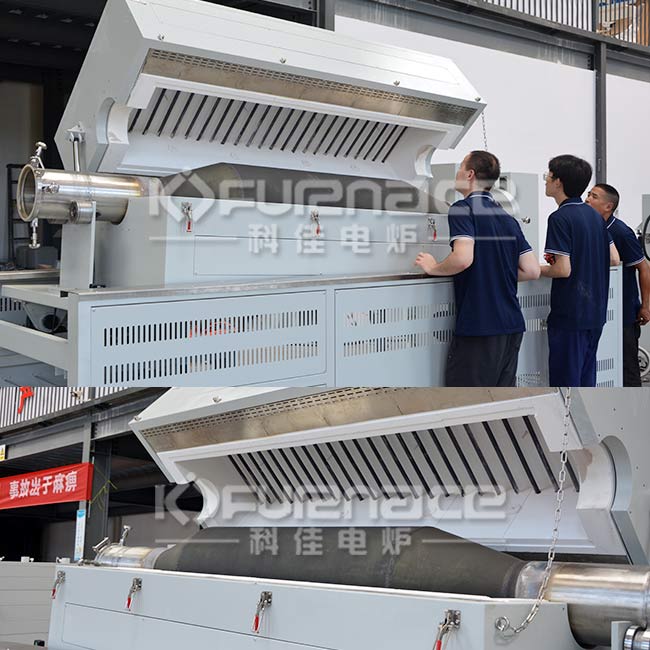